‘Greenfield project’, sounds different right?
There are things we might not be very familiar with, but its essentialism prods us to look towards it. Today it’s important to turn our face towards development as the world is changing at a very rapid pace, and Greenfield development is a concept in urbanization that leads us towards progress and advancement.
Greenfield development indicates the course of action for a new structure or construction on a plot of land that has never been a witness to any progress. The Greenfield sites can be compared to the act of painting on a blank canvas that is non-inclusive of the uninhibited impacts from the previous advancement project. This may consist of existing infrastructures, services, and buildings.
Greenfield regions are generally undeveloped areas that are advocated for production for the first time. The Greenfield developments eventually help to occupy those precious pieces of land that have no or little contamination since there is an absence of any kind of structures on the premises. Furthermore, there are no costs entailed in the remediation of the environment in the Greenfield sites. The sites are nearly ready for the construction of a building right away. As there is little or no usage of the land, there is no presence of any toxic chemicals in it, in addition to it if the site is situated at the edge of a city, then there is a huge capacity for expansion in the future as well.
Advantages of the Greenfield Development
- The major benefits of Greenfield Development are defined below.
- It caters to the design flexibility for meeting the requisites of particular projects
- The timelines for the construction happen at a much faster rate
- Huge areas are available to build anything that the client wants
- All the projects of the Greenfield development are highly cost-effective
- Another important aspect is that it does not disrupt the residents
- A better method of planning for the project can be executed due to the availability of open land
- There is no problem with the sizing of the property
In India, Greenfield projects have immerged to be a great help in the Make in India campaign. Not only does it provide the push for Aatmanirbhar Bharat but it provides job opportunities and solutions to various problems of the second-most populous country in the world. From Songdo in South Korea; Belmont, Arizona to Bihar in India, Greenfield projects have taken sustainable development to the next level.
Whenever we talk of Greenfield Project, one name that emerges as one of the best examples on this front would be the Wabtec Greenfield Project in Bihar.
Glossing over the last decade, we find that Wabtec has upgraded more than 2,000 locomotives for close to 40 customers around the world, and the company has strong orders for modernization from railroad operators like Norfolk Southern and Canadian Pacific. Wabtec has a long history of innovation, stretching from the first electric locomotives to the first freight locomotive that meets the U.S. government’s strict Tier 4 emission standards.
The year 2015, saw a $2.5 billion contract being signed between GE Transportation (a Wabtec company) and the Indian Railways to produce 1,000 Diesel Electric locomotives on a joint venture model. Under the partnership, 100 locomotives with 4500 – 6000 horsepower (HP) had to be supplied to the Indian Railways every year for 10 years. This flagship ‘Make in India’ project was India’s first big-ticket foreign direct investment in railways. Once operational, the factory would have an integrated eco-system of about 60 local and 10 global suppliers with a localized setup. Taking the vendors into account, it was estimated that a total of 4,000 new jobs would be created. Mindboggling, isn’t it?
We were lucky enough to get a chance to have a conversation with the head of the plant.
Eager to know what transpired, lets know more about the project through Shankar Dhar, Plant Head, Wabtec,
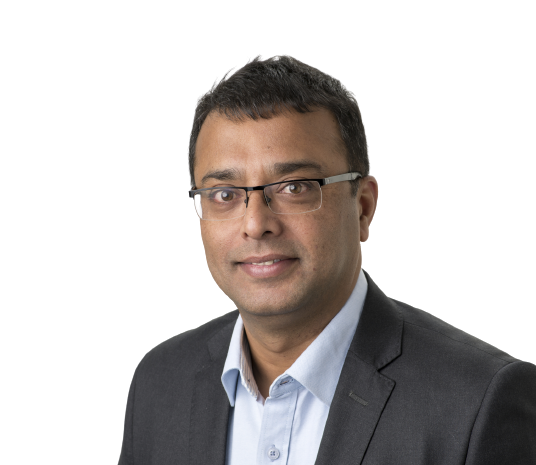
- How difficult is it to start a Greenfield project where everything has to start from scratch?
Literal examples of Greenfield projects are new factories, power plants, airports which are built from scratch on Greenfield land. In transportation industries (e.g., automotive, aircraft, engines) the equivalent concept is called “clean-sheet design”.
- What are the challenges you had to face?
As an ambitious project will have it, we did face several roadblocks. The factory that would produce these units had to be set up at Marhowra, a distant town in Bihar. Not only did the land regularly flood during the rainy season, but the site location could also only be reached by narrow roads over a three-hour journey from Patna. In addition to this, there were land compensation issues that needed to be negotiated.
But these early challenges were resolved over time. The groundbreaking of the factory construction started in June 2016, and by September 2018, phase – I of the plant was ready.
- What are your CSR (CORPORATE SOCIAL RESPONSIBILITIES)?
A community development program was set up for the 12 nearby villages. A baseline study was conducted which gave us a clear picture of our community volume and its need. The first thing that we started was the health care program where a permanent healthcare clinic was set up in Tejpurwa village. Vocational training centers for women named ‘Swabhiman’ were set up to up-skill women and help them to get self-employed by learning new skills. There is another program that aims at providing equity in our education system. This initiative is known as Sah Shikha Programme. Under this flagship, voluntary employees of our project go to the local schools to teach the students.
- Tell us about the merger of GE with Wabtec
GE completed the spinoff and merger of its Transportation business with Wabtec Corporation in 2019. GE received approximately $2.9 billion in cash as well as shares of Wabtec common stock and Wabtec nonvoting convertible preferred stock that together represent an approximately 24.9 percent ownership interest in Wabtec. GE shareholders own about 24.3 percent of Wabtec on a fully diluted basis.
The combined company now has approximately 27,000 employees in 50 countries. It is based in Wilmerding, Pennsylvania. The deal was actually like a once-in-a-lifetime opportunity to assemble nearly four centuries of combined experience to create a technologically advanced leader with a highly harmonizing set of potentials to improve the world.
- How relevant is the Make in India campaign?
The engagement and involvement of all concerned stakeholders in the company’s affairs help to reduce and uncover the project risks. Such two-way interactions help pave way for mutually beneficial newer ideas, improvement areas, and project-related expectations. The contract between Wabtec and the Indian Railways was India’s first big-ticket foreign direct investment in railways. The locally outsourced manpower and infrastructure was a huge boost to the plans of ‘Make in India’
- Any data you’d like to share regarding the production process that highlights the success of the project?
The world-class factory under the Make in India project became operational in September 2018. More than 70 percent of the employees were from the local region, and about 70 percent were local suppliers. The plant made sure to care for the environment too and boasts of 1 MW solar power, STP, and compost unit. There is a nearly 25% diversity mix, with women working in the factory and operating and handling the production process for which we are reaping benefits. 300+ engineers from India and abroad have worked on the design and manufacture of the ‘Make in India’ locomotive.
- How is this project strategically important for Indian Railway?
On November 9, 2015, the Ministry of Railways awarded the contracts for the Madhepura project and Marhaura project to Alstom and Wabtec respectively in a collective amount of US $6 billion. This multi-crore rupees deal was seen as the country’s first FDI in the railway sector. The production of 1000 high-power freight locomotives for 10 years designed to run on Indian railway tracks was an ambitious project indeed. And to supply nearly 120 locomotive engines per year was a record by itself.
- Kindly throw light on the RTD model adopted by Wabtec
Intending to find local talent, the HR team scouted over 20 colleges across Bihar, UP, Jharkhand, and Orissa. 200 students with diplomas from leading polytechnic colleges were identified for the position of Graduate Engineer Trainees. Once recruited, students were put through a finishing school under a ‘Recruit-Train-Deploy’ (RTD) model. To upskill students, this three-way synergy between the state and central government, the industry as well as the educational institutions contributed to the success of the program
- Why was there a plan to recruit students in the ambitious locomotive plant in Bihar?
The objective first was on finding local talent. Students have the knowledge, but once they get a job, they’re far more confident. The learning quotient of the students went up when they were assured of a job. One could see a level of sincerity among students that one can’t observe in the training programs otherwise. Students bring in fresh energy and new ideas that help develop the project even further.
- What was the shift in the lives of the employees that were observed?
The company has built 100 housing units inside the campus for employee accommodation; some of these are prioritized for women employees. Given the total workforce size, some male employees stay in town, where there are challenges with electricity and quality accommodation. One of the biggest success stories in establishing the Marhowra plant is the qualitative shift in the lives of the staff that produces close to eight locomotives a month –their individual stories from the selection, to training and finding a voice and the confidence to work on the factory floor – is a testament to the concerted effort of multiple stakeholders and institutions that converged to make in India.
By: Mobani Biswas